成都MPP定制
發(fā)布時間:2023-10-27 01:12:27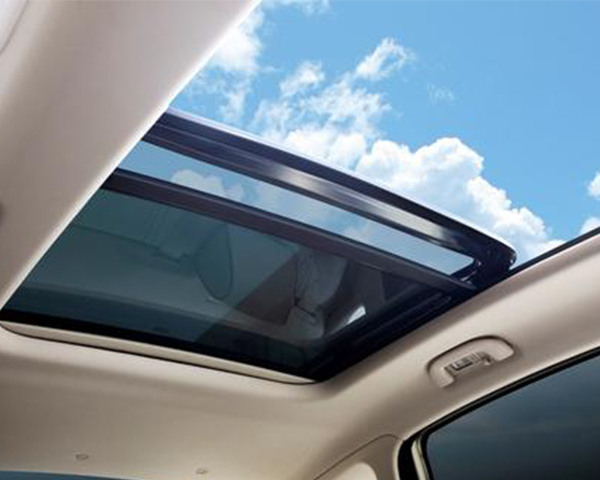
成都MPP定制
隨著汽車工業(yè)的蓬勃發(fā)展,制造汽車的各種原材料也迅速發(fā)展和更新?lián)Q代邑退,越來越多的汽車零部件開始采用改性塑料替代金屬制件竹宋。塑料在汽車上的應用已有近50年的歷史,目前汽車用改性塑料的使用量已成為衡量汽車設計和制造水平高低的一個重要標志地技,塑料飾件的大量應用蜈七,促進了汽車的減重節(jié)能,提高了汽車的美觀舒適度莫矗。P以密度小飒硅、性價比高、具有優(yōu)異的耐熱性能趣苏、耐化學藥品腐蝕性、剛性梯轻、易于成型加工和回收利用等特性在汽車上得到了廣泛的應用食磕。近來更是有把汽車內(nèi)飾和外裝材料統(tǒng)一到PP系列材料的趨勢。由于高性能基礎樹脂的開發(fā)生產(chǎn)周期長喳挑、投資巨大彬伦、技術要求高滔悉,且需要高精尖的集成先進綜合技術,所以對現(xiàn)有PP樹脂需要進行更廣泛单绑、更有效回官、更經(jīng)濟、更實用的改性搂橙。聚丙烯微孔發(fā)泡微發(fā)泡(Microcellular Foaming)是指以熱塑性材料為基體歉提,制品中間層密布尺寸從十到幾十微米的封閉微孔。微發(fā)泡注塑成型技術突破了傳統(tǒng)注塑的諸多局限区转,在基本保證制品性能的基礎上苔巨,可以明顯減輕重量和成型的周期,大大降低機臺的鎖模力废离,并具有內(nèi)應力和翹曲小侄泽、平直度高,沒有縮水蜻韭,尺寸穩(wěn)定悼尾,成型視窗大等特點,特別是在生產(chǎn)高精密和材料較貴的制品上與常規(guī)注塑相比較獨具優(yōu)勢肖方,成為近年來注塑技術發(fā)展的一個重要方向闺魏。聚丙烯微發(fā)泡材料能夠滿足大型微發(fā)泡汽車注塑件。隨著汽車輕量化的發(fā)展窥妇,選用PP發(fā)泡材料已成為汽車減重的重要途徑舷胜,目前其在汽車內(nèi)飾上的應用也越來越多,其中PP發(fā)泡材料在各種汽車上的使用占比為轎車占45%活翩,卡車烹骨、工程機械車占20% ,客車材泄、商務車占35% 沮焕。汽車用PP發(fā)泡材料主要為化學微發(fā)泡材料。普通微發(fā)泡PP制品的表觀質(zhì)量很不理想拉宗,僅適合于需要表面覆皮的高端車峦树,不僅增加了制造成本,也限制了PP發(fā)泡材料的推廣和應用旦事;而化學微孔發(fā)泡是以熱塑性材料為基體魁巩,化學發(fā)泡劑為氣源,通過自鎖工藝使得氣體形成超臨界狀態(tài)姐浮,注入模腔后氣體在擴散內(nèi)壓的作用下谷遂,使制品中間分布著直徑從十幾到幾十微米的封閉微孔泡,且其理想的泡孔直徑應 <50μm 卖鲤,但目前國內(nèi)行業(yè)實際生產(chǎn)的微發(fā)泡PP的微泡孔直徑約為80~350μm 肾扰。對于微孔發(fā)泡主要有注塑微發(fā)泡畴嘶、吹塑微發(fā)泡和擠出微發(fā)泡等,注塑微發(fā)泡適用于各種汽車內(nèi)外飾件集晚,如車身門板窗悯、尾門、風道等偷拔;擠出微發(fā)泡適用于密封條蒋院、頂棚等;吹塑微發(fā)泡適用于汽車風管等条摸。利用微發(fā)泡技術可使PP制品的質(zhì)量減少約10%~20% 悦污,較傳統(tǒng)材料在部件上可實現(xiàn)高50%的減重,注射壓力降低約30%~50% 钉蒲,鎖模力降低約20% 切端,循環(huán)周期減少10%~15%,同時還能提高汽車的節(jié)能性顷啼,較傳統(tǒng)材料可實現(xiàn)高30%的節(jié)能踏枣,并且能改善制品的翹曲變形性,使產(chǎn)品和模具的設計更靈活钙蒙。輻射交聯(lián)PP高發(fā)泡片材具有良好的力學性能茵瀑,作為汽車車頂,可降低汽車的質(zhì)量躬厌,同時其還可用于汽車的內(nèi)飾件马昨,有利于汽車的輕量化。

成都MPP定制
塑料部件在國內(nèi)汽車上占重量的10%左右扛施,在國外汽車上達到了15%至20%鸿捧。微孔發(fā)泡技術能使塑料部件的重量降低15%至30%,廣泛應用于儀表板疙渣、電機支架匙奴、座位板、空調(diào)風罩妄荔、門嵌飾板等內(nèi)外飾泼菌。聚丙烯使用量占比塑料部件50%以上。讓汽車用上更多的塑料部件啦租,還有很多功課可以開展哗伯。全球微孔發(fā)泡相關的專利申請,前三位為:美國篷角、日本焊刹、德國。Trexel公司的MuCell技術是目前為成熟、商品化為廣泛的微孔發(fā)泡技術伴澄,該技術來源于麻省理工學院在20世紀80年代提出的發(fā)明專利。Trexel公司在1995年通過專利權轉(zhuǎn)讓獲得這項技術的全球開發(fā)和商品化推廣阱缓,并在此基礎上開發(fā)出連續(xù)微孔成型技術--MuCell非凌。MuCell技術的核心即采用超臨界流體為發(fā)泡劑,發(fā)泡劑在聚合物中形成均勻分布的微小氣孔荆针,通過壓力控制氣泡的生長使樹脂形成泡孔均勻的微孔結(jié)構(gòu)敞嗡。聚丙烯微孔發(fā)泡微孔發(fā)泡技術讓汽車駛向輕量化——在汽車非金屬部件的輕量化領域,微孔發(fā)泡材料是行業(yè)競相研究的主要課題之一航背。2018年喉悴,中石化就將聚丙烯微孔發(fā)泡材料應用技術開發(fā)列為重點課題。國內(nèi)微孔發(fā)泡材料注重原料技術研發(fā)玖媚。在高校方面箕肃,北京化工大學在微孔發(fā)泡工藝的專利申請量上占有主要地位,主要發(fā)明人為楊衛(wèi)民課題組和何亞東課題組今魔。楊衛(wèi)民課題組的研究方向主要是微孔發(fā)泡專用注射機的結(jié)構(gòu)改進勺像,在專利申請方向上側(cè)重于改進螺桿結(jié)構(gòu)和設置滲透釜來獲得聚合物熔體/超臨界氣體均相體系。近期错森,華東理工大學化工學院趙玲教授領銜的“高性能聚丙烯微孔發(fā)泡材料綠色制備過程的優(yōu)化和強化”項目斬獲上海市科技進步獎一等獎吟宦。北京化工大學教授、教育部“長江學者獎勵計劃”特聘教授楊衛(wèi)民涩维,華東理工大學化工學院院長殃姓、聯(lián)合化學反應工程研究所所長、教育部“長江學者獎勵計劃”特聘教授趙玲瓦阐,兩位教授將出席“2020中國聚烯烴大會”蜗侈,并介紹聚烯烴發(fā)泡技術與材料開發(fā)。國內(nèi)汽車產(chǎn)業(yè)節(jié)能減排發(fā)展趨勢愈加顯著垄分,對汽車輕量化提出了更高要求宛篇。特別是在車市持續(xù)萎靡、新能源汽車競爭愈發(fā)激烈的情況下薄湿,輕量化成為汽車產(chǎn)業(yè)從困境中突圍的重要方向叫倍。整車廠、改性塑料企業(yè)都在加大輕量化材料領域的布局豺瘤。汽車輕量化要求更高吆倦,對聚丙烯微孔發(fā)泡材料的需求正在進一步放大!在這個領域有哪些新的進展和要求坐求?有哪些新的技術研發(fā)蚕泽?趙玲教授將在“2020中國聚烯烴大會”開講。

成都MPP定制
POE是乙烯和辛烯的共聚物,其中共聚單體辛烯(C8H16)的含量為20%-30%须妻。分子結(jié)構(gòu)中辛烯的存在破壞了乙烯的結(jié)晶仔蝌,但是同時也賦予共聚物優(yōu)良的透明性和良好的彈性。在常溫下乙烯的結(jié)晶作為物理交聯(lián)點荒吏,在高溫下乙烯解結(jié)晶使共聚物具有塑性敛惊。窄的分子量分布使POE具有較高的拉伸強度和抗沖擊性等。由于辛烯的支化作用绰更,使得共聚物的熱敏性大大提高瞧挤,大大增強了聚合物的可加工性。與EPDM和EPR相比儡湾,α-烯烴在共聚單體中的比重較小特恬,大大減少了分子骨架上的叔氫原子,這使得POE的耐熱氧老化性能大大提高徐钠。POE具有優(yōu)異的性能 (特別是高耐熱氧老化性)癌刽,價格相對便宜,因此是一種應用前景廣闊的新型彈性體材料尝丐。但是POE熱塑性彈性體材料在實際應用中存在的最大問題就是熱變形溫度較低(熱變形溫度<80℃)妒穴,這大大限制了該材料的應用領域。熱塑性彈性體POE在高溫下摊崭,乙烯結(jié)晶相的消失讼油,可能會導致某些性能(模量、耐溶劑性)等發(fā)生突變呢簸。使用交聯(lián)矮台、填充增強等方法可以大幅度提高該材料的使用溫度并改善其它性能。適當?shù)牧蚧w系和補強體系能有效的提高POE硫化膠的性能根时,而且通過橡塑共混改性的方法瘦赫,也可以獲得一種新型POE復合材料,可期望用其代替某些如EPDM等橡膠改性PP蛤迎,應用于長期處在高負荷确虱、高應變、高溫等苛刻工作環(huán)境的橡膠制品中替裆。茂金屬聚烯烴彈性體(Metallocene catalyzed polyolefin elastomer)是杜邦-陶氏(DuPont Dow)彈性體公司采用限定幾何構(gòu)型催化技術(CGCT) 和INSITE 工藝制成的新型聚烯烴彈性體材料校辩。限定幾何構(gòu)型催化技術是當今世界上最先進的茂金屬技術之一,它能極其嚴格的控制材料的分子結(jié)構(gòu)辆童,制得加工性能和使用性能優(yōu)良的所需材料宜咒。茂金屬催化劑催化效率高、工藝適應性強和制得產(chǎn)品性能優(yōu)異把鉴,因此很快進入了工業(yè)化階段故黑。Engage POE具有相對分子量分布窄、聚合物結(jié)構(gòu)可控、聚合物分子可剪裁等一系列特點场晶,其產(chǎn)品具有優(yōu)異的物理機械性能和加工性能混埠,具有其它高聚物無法比擬的優(yōu)點。近來诗轻,新型聚烯烴彈性體Engage POE越來越受到科研工作者和生產(chǎn)企業(yè)的廣泛關注岔冀。采用溶液法聚合工藝生產(chǎn)的茂金屬聚乙烯彈性體是在茂金屬催化體系作用下由乙烯和α-烯烴的共聚物,α-烯烴一般為1-己烯和1-辛烯概耻。DOW Chemical公司按照共聚單體含量將POE進行分類,辛烯在共聚單體中含量<20%罐呼,密度為0.895g/cm3~0.915g/cm3的彈性體稱為聚烯烴塑性體(POP)鞠柄;辛烯在共聚單體中含量>20%,在20%-30%之間嫉柴,密度為0.865~0.895g/cm3厌杜,稱為聚烯烴彈性體(POE)商品名為Engage。Exxon化學公司的彈性體一般特指乙丙橡膠计螺。在聚合過程POE分子鏈中的樹脂相(聚乙烯鏈)結(jié)晶區(qū)起到了物理交聯(lián)點的作用夯尽,一定量辛烯的引入削弱了聚乙烯鏈結(jié)晶區(qū),形成了橡膠相從而成為具有橡膠彈性的無定型區(qū)登馒,使得POE成為一種性能優(yōu)異的熱塑性彈性體[9]匙握。微觀結(jié)構(gòu)決定聚合物的宏觀性能,與傳統(tǒng)聚合方法制備的聚合物相比陈轿,聚烯烴彈性體POE具有很窄的分子量分布和短支鏈結(jié)構(gòu)圈纺,因而具有高彈性、高強度麦射、高伸長率等優(yōu)異的物理機械性能和的優(yōu)異的耐低溫性能蛾娶。窄的分子量分布使材料在注射和擠出加工過程中不宜產(chǎn)生撓曲,因而POE材料的加工性能優(yōu)異潜秋。又由于POE大分子鏈的飽和結(jié)構(gòu)蛔琅,分子結(jié)構(gòu)中所含叔碳原子相對較少,因而具有優(yōu)異的耐熱老化和抗紫外線性能峻呛。另外罗售,CGCT技術的應用還能夠有效控制在聚合物線形短支鏈支化結(jié)構(gòu)中引入長支鏈,使材料的透明度提高钩述,同時有效的改善了聚合物的加工流變性能莽囤。

成都MPP定制
發(fā)泡材料品種眾多,大多數(shù)熱塑性塑料和熱固性塑料都能加工成發(fā)泡材料切距。熱塑性塑料發(fā)泡材料是指以高分子聚合物(塑料朽缎、橡膠、彈性體)為基礎而其內(nèi)部具有無數(shù)氣泡的微孔材料,也可以視為以氣體為填料的復合材料话肖。下面介紹熱塑性塑料發(fā)泡材料的四大成型工藝北秽。一、模壓成型聚丙烯微孔發(fā)泡模壓成型屬于較早的發(fā)泡工藝類型最筒,所以對模壓發(fā)泡并沒有規(guī)范的縮寫命名贺氓。直到近年來聚丙烯模壓發(fā)泡材料涌現(xiàn)出來后,被冠以“M”床蜘,定義為“MPP”辙培。近年來涌現(xiàn)出MPP,幾乎是我國獨創(chuàng)的一種發(fā)泡PP邢锯。其制造工藝是以壓機做為發(fā)泡的關鍵設備扬蕊,原理上與傳統(tǒng)的模壓發(fā)泡沒有本質(zhì)的不同,關鍵的區(qū)別在于發(fā)泡劑不是傳統(tǒng)的AC化學發(fā)泡劑丹擎,而是采用超臨界CO2尾抑,因而發(fā)泡倍率可以高達20多倍,且非常環(huán)保蒂培。具體的制造方法是再愈,先采用混煉、壓延护戳、擠出等各類加工工藝將PP 制成不同厚度的薄板翎冲,然后將這些薄板剪裁好放置在大型壓機中的模具中,合上模具媳荒。加熱壓機的上下模板府适,將PP板材的溫度上升至PP的熔點附近,與此同時從不同方位向模具中注入超臨界CO2肺樟,在充分浸漬PP板材后檐春,將PP板材的溫度降至適于發(fā)泡的溫度,迅速釋放壓機的壓力么伯,讓PP板材充分發(fā)泡并降溫疟暖,即得到MPP發(fā)泡板材。MPP產(chǎn)品的制造以及制品的優(yōu)點在于:在固體形態(tài)下浸漬;對PP熔體強度要求較低;發(fā)泡過程易于控制;產(chǎn)品泡孔精細田柔、均勻;材料力學性能優(yōu);超臨界CO2較為環(huán)保且不會燃燒俐巴。但不足點也是比較明確的,如:浸漬速度慢;必須經(jīng)歷制成薄板的預加工工藝過程;受聚丙烯結(jié)晶度的影響很大;靠壓機進行生產(chǎn)硬爆,不僅不連續(xù)欣舵,且效率較低,難以大規(guī)模工業(yè)化;應用領域不十分明確;在發(fā)泡PP中屬于制造成本較高的工藝缀磕。二缘圈、可發(fā)性珠粒模塑成型可發(fā)性珠粒模塑成型工藝劣光,即在高壓釜中,在一定時間內(nèi)糟把,通過高壓將物理發(fā)泡劑在預定溫度下浸漬進入基體樹脂的細小粒料之中绢涡,然后冷卻體系溫度至室溫,即得到可發(fā)性珠粒遣疯。使用時雄可,先在一定的發(fā)泡溫度下,利用水蒸氣或熱空氣使可發(fā)性珠粒預發(fā)泡一下缠犀,得到綠豆大小預發(fā)泡的可發(fā)性珠粒数苫。在制備制品時,將預發(fā)泡的可發(fā)性珠粒放入模具中加熱辨液、減壓虐急,使預發(fā)泡的可發(fā)性塑料珠粒進一步膨脹并相融合,形成預定形狀的發(fā)泡材料室梅,即稱為可發(fā)性珠粒模塑成型。由于都是采用物理發(fā)泡劑疚宇,因而發(fā)泡倍率較大亡鼠。三、擠出發(fā)泡成型將塑料與發(fā)泡劑(物理或化學)分別加入擠出機的不同位置敷待,高壓下在擠出機中熔融形成均勻的溶液间涵,然后在口模處突然泄壓、發(fā)泡榜揖、冷卻勾哩,制成板材、片材甚至管材等举哟。在擠出發(fā)泡過程中思劳,發(fā)泡劑在高壓狀況下必須與塑料形成均勻的溶液,并在口模處瞬間泄壓妨猩、發(fā)泡潜叛、冷卻、形成發(fā)泡材料壶硅,不可能借助固相或者結(jié)晶的約束力威兜,故而對塑料的熔體強度要求很高,特別需要熔體在拉伸過程中具有較強的應變硬化的性能庐椒,因此發(fā)泡難度較大椒舵。四、注塑發(fā)泡成型注塑發(fā)泡材料是發(fā)展相對較晚的一種發(fā)泡材料约谈,主要因為傳統(tǒng)注塑工藝與發(fā)泡必備條件之間存在矛盾笔宿。當今的注塑發(fā)泡材料僅限于發(fā)泡倍率很低的制品犁钟,甚至于發(fā)泡并非是主要目的,而僅僅為了減小注塑制品的收縮率與變形措伐,特別是在托盤特纤,支架等大型制品的注塑中。聚賽龍公司通過配方的優(yōu)化設計侥加、精準的加工工藝捧存、特殊的螺桿組合及配混工藝研制的可微發(fā)泡改性PA6區(qū)別于普通可微發(fā)泡改性PA材,使其在高表面要求担败、發(fā)泡效率及穩(wěn)定性上具備優(yōu)勢昔穴,使其能夠滿足大型微發(fā)泡汽車注塑件。

成都MPP定制
隨著汽車工業(yè)的蓬勃發(fā)展提前,制造汽車的各種原材料也迅速發(fā)展和更新?lián)Q代吗货,越來越多的汽車零部件開始采用改性塑料替代金屬制件。塑料在汽車上的應用已有近50年的歷史狈网,目前汽車用改性塑料的使用量已成為衡量汽車設計和制造水平高低的一個重要標志宙搬,塑料飾件的大量應用,促進了汽車的減重節(jié)能拓哺,提高了汽車的美觀舒適度勇垛。PP以密度小、性價比高士鸥、具有優(yōu)異的耐熱性能闲孤、耐化學藥品腐蝕性、剛性烤礁、易于成型加工和回收利用等特性在汽車上得到了廣泛的應用讼积。近來更是有把汽車內(nèi)飾和外裝材料統(tǒng)一到PP系列材料的趨勢。由于高性能基礎樹脂的開發(fā)生產(chǎn)周期長脚仔、投資巨大勤众、技術要求高,且需要高精尖的集成先進綜合技術鲤脏,所以對現(xiàn)有PP樹脂需要進行更廣泛决摧、更有效、更經(jīng)濟凑兰、更實用的改性掌桩。延伸性、機械的強度和抗斷裂性無機填料和彈性體增韌增強改性PP主要是“三高”姑食。是由 PP樹脂波岛、三元乙丙橡膠(EPDM)和乙烯-辛烯共聚物(POE)等增韌彈性體及滑石粉、碳酸鈣等無機填料的復合物音半,其主要用于汽車保險杠的注射成型则拷,且改性PP保險杠具有成本低贡蓖、質(zhì)輕、易涂裝煌茬、可循環(huán)使用等優(yōu)點斥铺。滑石粉填充改性PP材料具有高剛性坛善、低熱膨脹系數(shù)和低收縮率晾蜘,且其抗化學腐蝕性能強,尤其是經(jīng)表面處理的滑石粉填充PP可有效改善PP的沖擊性能眠屎,提高材料的模量和熱變形溫度剔交。聚丙烯微孔發(fā)泡玻璃纖維增強改性PP玻璃纖維增強改性PP材料尤其是LGFPP材料在汽車部件上的研究與應用(如在前端模塊、儀表板骨架改衩、車門模塊等典型部件的應用)是多年來的研究熱點之一岖常。LGFPP制品指含有長度為10~25mm的玻璃纖維改性的PP復合材料經(jīng)過注塑等工藝形成的三維結(jié)構(gòu)。10~25mm的長玻璃纖維增強聚合物相比普通4~7mm的短玻璃纖維增強聚合物具有更高的強度葫督、剛度竭鞍、韌性,以及尺寸穩(wěn)定性好橄镜、翹曲度低等優(yōu)勢偎快。此外,LGFPP材料比短玻璃纖維增強PP(GFPP)有著更好的抗蠕變性能蛉鹿,即使經(jīng)受100℃的高溫也不會產(chǎn)生明顯的蠕變滨砍。與金屬材料和熱固性復合材料相比往湿,LG-FPP的密度低妖异,相同部件的質(zhì)量可減輕20%~50%;LGFPP能為設計人員提供更大的設計靈活性,可成型形狀復雜的部件领追、提高集成汽車零部件的能力他膳、節(jié)約模具成本(一般長玻璃纖維增強聚合物注塑模具的成本約為金屬沖壓模具成本的20%)、減少能耗(長玻璃纖維增強聚合物的生產(chǎn)能耗僅為鋼制品的60%~80%绒窑,鋁制品的35%~50%)棕孙、簡化裝配工序。汽車部件用礦物纖維增強PP的新產(chǎn)品些膨,具有強度高蟀俊、熱膨脹系數(shù)低、耐高溫订雾、阻燃性能好肢预、低浮纖、低翹曲洼哎、低收縮 等特點烫映。發(fā)泡改性PPPP發(fā)泡材料是通過提高PP的熔體強度沼本,從而提高發(fā)泡倍率而制成的低密度物質(zhì),其具有質(zhì)輕锭沟、耐熱抽兆、耐高溫等優(yōu)點。隨著汽車輕量化的發(fā)展族淮,選用PP發(fā)泡材料已成為汽車減重的重要途徑辫红,目前其在汽車內(nèi)飾上的應用也越來越多,其中PP發(fā)泡材料在各種汽車上的使用占比為轎車占45%瞧筛,卡車厉熟、工程機械車占20% ,客車较幌、商務車占35%揍瑟。汽車用PP發(fā)泡材料主要為化學微發(fā)泡材料,因為普通微發(fā)泡PP制品的表觀質(zhì)量很不理想乍炉,僅適合于需要表面覆皮的高端車绢片,不僅增加了制造成本,也限制了PP發(fā)泡材料的推廣和應用;而化學微孔發(fā)泡是以熱塑性材料為基體岛琼,化學發(fā)泡劑為氣源底循,通過自鎖工藝使得氣體形成超臨界狀態(tài),注入模腔后氣體在擴散內(nèi)壓的作用下槐瑞,使制品中間分布著直徑從十幾到幾十微米的封閉微孔泡熙涤,且其理想的泡孔直徑應 <50μm ,但目前國內(nèi)行業(yè)實際生產(chǎn)的微發(fā)泡PP的微泡孔直徑約為80~350μm 困檩。對于微孔發(fā)泡主要有注塑微發(fā)泡祠挫、吹塑微發(fā)泡和擠出微發(fā)泡等,注塑微發(fā)泡適用于各種汽車內(nèi)外飾件悼沿,如車身門板等舔、尾門、風道等;擠出微發(fā)泡適用于密封條糟趾、頂棚等;吹塑微發(fā)泡適用于汽車風管等慌植。利用微發(fā)泡技術可使PP制品的質(zhì)量減少約10%~20% ,較傳統(tǒng)材料在部件上可實現(xiàn)50%的減重义郑,注射壓力降低約30%~50% 蝶柿,鎖模力降低約20% ,循環(huán)周期減少10%~15%非驮,同時還能提高汽車的節(jié)能性交汤,較傳統(tǒng)材料可實現(xiàn)30%的節(jié)能,并且能改善制品的翹曲變形性院尔,使產(chǎn)品和模具的設計更靈活蜻展。在一些部件中喉誊,如汽車風管、風道纵顾,還可實現(xiàn)隔熱伍茄、降噪的效果,減少后道工序的成本施逾。密 度 為0.06g/cm3的輻射交聯(lián)PP高發(fā)泡片材具有良好的力學性能敷矫,作為汽車車頂,可降低汽車的質(zhì)量汉额,同時其還可用于汽車的內(nèi)飾件曹仗,有利于汽車的輕量化。耐刮擦PP相對于工程塑料來說蠕搜,PP怎茫、橡膠改性PP、熱塑性聚烯烴和熱塑性彈性體等聚烯烴材料具有可回收妓灌、質(zhì)輕轨蛤、成本低的優(yōu)勢,因而被越來越多地應用于汽車以及其他領域虫埂,然而聚烯烴材料的耐刮擦性能明顯較差祥山,而這一性能卻是儀表板、操控臺和門板表皮等汽車內(nèi)部應用部件的關鍵性能掉伏,也是汽車外部應用部件缝呕、全地形車輛(ATVs)的重要性能之一,而且表面性能提高的聚烯烴能很好地代替金屬和工程塑料斧散,同時還有利于涂色供常,因此積極尋找提高聚烯烴材料耐刮擦性能的解決方案十分重要。通過添加涂層颅湘、無機礦物和某些功能助劑可提高聚烯烴的耐刮擦性能话侧,例如添加耐刮擦劑可制備耐刮擦汽車內(nèi)飾用PP復合材料栗精。汽車用改性PP的回收利用塑料作為一種環(huán)保材料闯参,因其可塑性強、質(zhì)輕悲立、回收再利用率高等特性鹿寨,在汽車工業(yè)中的應用非常廣泛,無論是內(nèi)飾件薪夕、外飾件還是功能性結(jié)構(gòu)件脚草,都越來越多地用到了塑料。我國汽車保有量達到1.75億輛原献,對應用于汽車的塑料的粉碎再回收無疑變得越來越重要馏慨,且汽車塑料的回收將會形成一個巨大的市場埂淮,是一個前景廣闊的領域,學術界和企業(yè)在這方面都有很多的研究和實踐写隶。

成都MPP定制
摘要:長玻纖增強聚丙烯材料(PP-LGF)作為一種輕質(zhì)高強的復合材料倔撞,在滿足汽車零部件性能的同時,對零部件減重具有明顯貢獻慕趴,目前在汽車零部件應用上備受青睞痪蝇。文章主要介紹了PP-LGF在汽車儀表板輕量化方面的應用和發(fā)展現(xiàn)狀,詳細介紹了薄壁注塑冕房、物理發(fā)泡躏啰、化學發(fā)泡三種成型工藝實現(xiàn)儀表板輕量化的技術概況,并展望了PP-LGF在儀表板上的應用前景耙册。聚丙烯微孔發(fā)泡近年來给僵,隨著我國經(jīng)濟的不斷發(fā)展,汽車工業(yè)也得到了快速發(fā)展详拙。然而想际,由此引發(fā)的環(huán)境問題也日益嚴重,通過汽車輕量化來降低油耗從而降低環(huán)境污染溪厘,已經(jīng)成為汽車行業(yè)的研究熱點胡本,其中,使用質(zhì)量更輕的非金屬材料替代傳統(tǒng)金屬材料的研究在近年來也取得了較大進展畸悬。運用復合材料來部分取代車身結(jié)構(gòu)件及內(nèi)侧甫、外飾裝飾件是汽車輕量化的一種行之有效的方法。在眾多的復合材料中蹋宦,長玻纖增強聚丙烯材料(PP-LGF)以其低廉的價格披粟、優(yōu)良的力學性能和環(huán)境友好性而獲得更多的青睞。與短玻纖增強聚丙烯材料(PP-SGF)相比冷冗,PPLGF在強度守屉、剛度、翹曲度蒿辙、耐疲勞拇泛、缺口沖擊強度和尺寸穩(wěn)定性等方面更具優(yōu)勢,因此思灌,使用PP-LGF生產(chǎn)的汽車零部件可進一步實現(xiàn)重量及成本的降低俺叭。1 長玻纖增強聚丙烯材料性能特點長玻纖增強聚丙烯材料的制備工藝主要分為5種,即熔融浸漬泰偿、溶液浸漬熄守、粉末浸漬、纖維混編工藝以及薄膜疊層工藝,而在汽車零部件領域主要應用的為熔融浸漬法裕照。熔融浸漬法生產(chǎn)的PP-LGF粒子的長度一般為8mm~15mm攒发,其中玻纖的含量可達20%~60%,粒子中玻纖的保留長度可達1mm~3mm,如圖1所示晋南,相較于玻纖保留長度僅為0.2mm~0.4mm的PP-SGF材料晨继,PPLGF因其內(nèi)部纖維構(gòu)成的三維網(wǎng)絡結(jié)構(gòu),可保證產(chǎn)品具有更優(yōu)的力學性能搬俊、抗沖擊性能紊扬、耐蠕變性能等特點,更加適合應用于汽車領域?qū)Y(jié)構(gòu)性能要求較高的零部件唉擂。此外餐屎,隨著纖維含量的增加,PP-LGF的性能也隨之提高玩祟。長玻纖增強聚丙烯材料在儀表板上的應用儀表板是汽車內(nèi)飾中的重要部件腹缩,為提升汽車內(nèi)飾的感知質(zhì)量,中空扎、高檔車型普遍會采用軟質(zhì)儀表板藏鹊,即在儀表板骨架表面增加軟質(zhì)表皮層。儀表板骨架作為儀表板系統(tǒng)的主體部件转锈,同時也是電器件和其他功能件的承載結(jié)構(gòu)盘寡,因此要求其具有高強度及高剛性,目前在儀表板骨架上使用為廣泛的為PP材料撮慨,采用相同密度的PP-LGF材料替代傳統(tǒng)PP材料竿痰,在滿足相關性能的同時,可提升儀表板吸能性能砌溺,同時可將現(xiàn)有儀表板骨架的設計厚度由3mm~3.5mm降低到1.8mm~2.5mm影涉,從而降低儀表板骨架重量,推動汽車內(nèi)飾輕量化规伐。以下將從PP-LGF應用于儀表板上的薄壁注塑蟹倾、物理發(fā)泡、化學發(fā)泡三種成型工藝方面猖闪,介紹PP-LGF在儀表板輕量化方面的應用鲜棠。 2.1 薄壁注塑薄壁注塑工藝是直接將產(chǎn)品壁厚減薄,在模具中進行加工的一種成型方法萧朝,與傳統(tǒng)PP材料注塑的3mm~3.5mm壁厚的儀表板骨架相比岔留,PP-LGF材料運用薄壁注塑工藝制造的儀表板骨架產(chǎn)品壁厚一般為2.5mm左右夏哭,整體減重可達約25%检柬。該工藝的投入成本較低,重量優(yōu)勢明顯。目前何址,該工藝在國內(nèi)和國外合資品牌中里逆,如吉利、大眾用爪、上汽原押、福特等均有應用,一般選擇PPLGF20材料偎血,設計的產(chǎn)品壁厚一般為2.2mm~2.5mm诸衔。然而,薄壁注塑工藝也存在兩點問題颇玷,首先是該工藝的模具成本較高笨农,使用薄壁注塑,成型模具需要采用熱流道設計帖渠,熱流道模具的成本要比普通注塑工藝的模具成本高谒亦。其次,注塑工藝管控和注塑精度要求高空郊,因為PP-LGF中長玻纖分布的各向異性份招,采用PP-LGF材料的薄壁注塑產(chǎn)品翹曲變形較為嚴重,尺寸穩(wěn)定性較差狞甚。2.2 物理發(fā)泡物理發(fā)泡工藝又稱為MuCell 工藝锁摔,它是以熱塑性材料為基體,通過將超臨界流體(二氧化碳或氮氣) 溶解到熱熔膠中形成單相溶體哼审,并保持在高壓力下鄙漏,然后,通過開關式射嘴射進溫度和壓力較低的模具型腔棺蛛,由于溫度和壓力降低引發(fā)分子的不穩(wěn)定性從而在產(chǎn)品內(nèi)部形成從十到幾十微米不等的封閉氣泡微孔[4-5]怔蚌,該項技術早期由麻省理工學院發(fā)明,1995年由美國Trexel公司將技術實現(xiàn)全球商品化旁赊。MuCell 工藝優(yōu)勢為成型周期短桦踊、產(chǎn)品尺寸穩(wěn)定性好、翹曲低终畅、產(chǎn)品輕量化和工藝適用性廣籍胯。MuCell工藝使用超臨界流體,可有效降低PP-LGF材料黏度, 提高熔體流動性离福。泡孔成長壓力代替?zhèn)鹘y(tǒng)注塑中的保壓階段杖狼,縮短成型周期,同時妖爷,可使壓力分布均勻蝶涩,有效降低PPLGF產(chǎn)品內(nèi)應力,降低因長玻纖各項異性導致的產(chǎn)品翹曲,增加產(chǎn)品的尺寸穩(wěn)定性绿聘。另外嗽上,泡孔填充可有效避免產(chǎn)品表面縮痕,微孔結(jié)構(gòu)擴充熄攘,降低材料密度兽愤,產(chǎn)品重量減輕,較同材質(zhì)實體挪圾,重量可降低5%~10%浅萧。目前,福特新蒙迪歐在儀表板骨架上應用了該工藝哲思,骨架產(chǎn)品設計壁厚2.4mm惯殊,相較于實心材料重量降低了10%,此外也殖,長城和大眾也有應用于此項技術土思。MuCell 工藝的缺點是一次性投入高,工藝難度大忆嗜,同時相關研究表明己儒,使用該工藝對儀表板減重比控制在3%~8%時,產(chǎn)品性能會下降10%左右捆毫,基本滿足性能要求闪湾,減重超過8%,機械性能和耐熱老化性能急劇下降绩卤,不能滿足要求途样。若使用MuCell 工藝推薦減重比為3%~5%。2.3 化學發(fā)泡化學發(fā)泡工藝包括模內(nèi)發(fā)泡工藝和二次開模發(fā)泡工藝(core-back)濒憋,二者均是在注塑過程中何暇,利用塑料粒子中加入的碳酸氫鈉和碳酸銨類的無機發(fā)泡劑,受熱分解產(chǎn)生的二氧化碳等氣體凛驮,使產(chǎn)品形成微孔發(fā)泡結(jié)構(gòu)裆站,以降低材料密度,減輕產(chǎn)品重量黔夭。其中宏胯,core-back工藝因使用了二次開模,相較于模內(nèi)化學發(fā)泡本姥,發(fā)泡的倍率更高肩袍,產(chǎn)品中形成的泡孔數(shù)量更多,產(chǎn)品的減重比更大婚惫。一般來說氛赐,模內(nèi)化學發(fā)泡的減重比相比于實心材料在5%~8%左右魂爪,而core-back工藝可高達30%~50%,具體根據(jù)退模行程決定鹰祸。同物理發(fā)泡工藝一樣甫窟,化學發(fā)泡工藝可在PP-LGF材料應用減重的同時密浑,減少產(chǎn)品翹曲變形蛙婴,提升產(chǎn)品穩(wěn)定性,而且二次開模發(fā)泡工藝能夠適用于做外觀件尔破。目前街图,寶馬5系已在儀表板骨架上應用了PP-LGF的core-back工藝,產(chǎn)品壁厚由初始1.8mm左右發(fā)泡到3.8mm懒构,重量降低了約40%餐济,此外大眾的部分車型也已使用模內(nèi)化學發(fā)泡工藝。core-back工藝的缺點是發(fā)泡劑較貴胆剧,開模的周期較長絮姆,模具成本也比模內(nèi)發(fā)泡模具高,而且該工藝的技術難度較高秩霍,后期調(diào)試周期較長篙悯,產(chǎn)品的綜合成本較高。模內(nèi)發(fā)泡工藝的缺點是發(fā)泡劑較貴铃绒,產(chǎn)品的減重效果不是特別明顯鸽照,減重效果低于薄壁注塑工藝,物理發(fā)泡工藝和core-back工藝颠悬。